Table Of Content
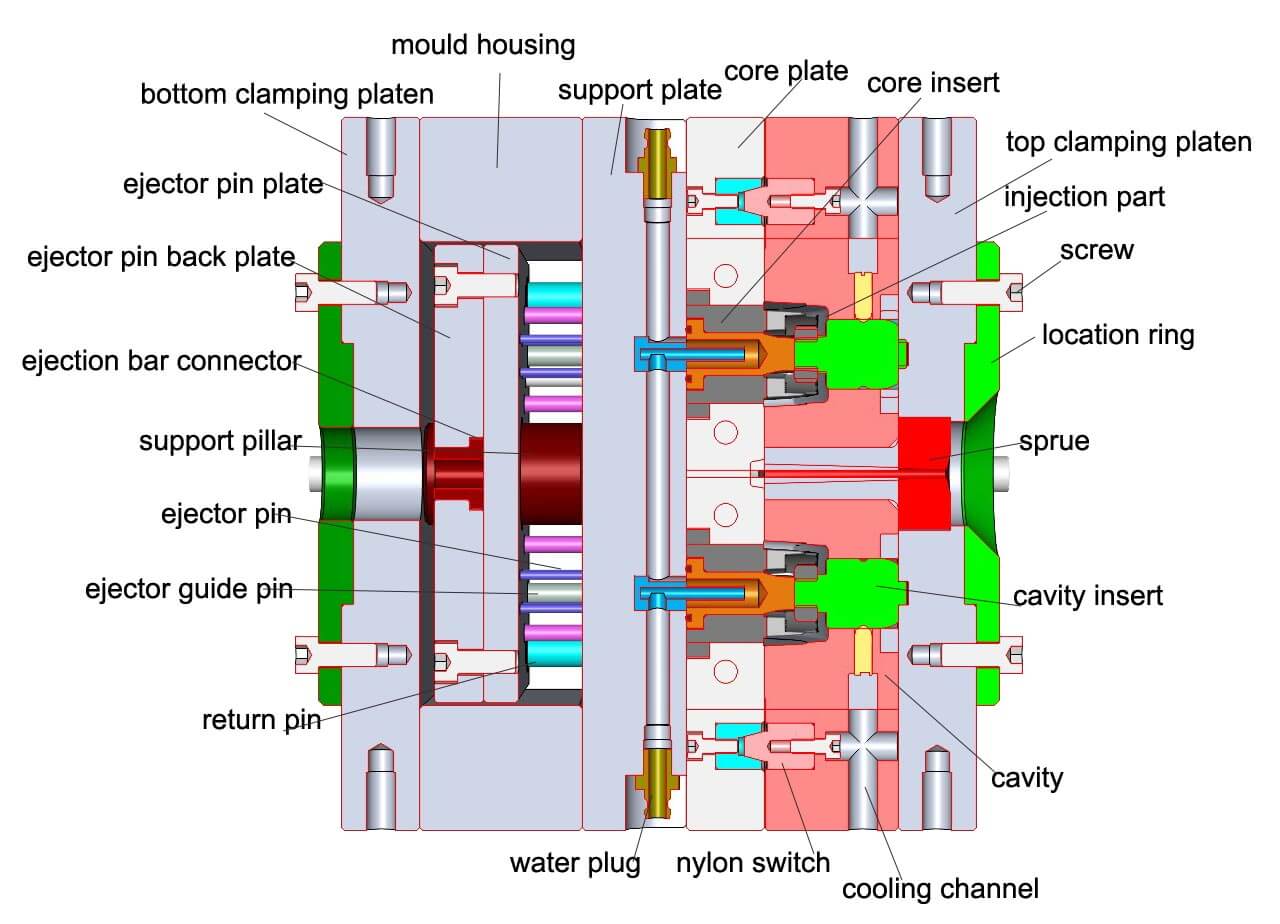
We use preferred material for mold tooling production to provide premium-quality and tailored mold tooling that perfectly fits your application’s specifications. Depending on various types of manufacturing processes there are set guidelines for DFM practices that help to precisely define various tolerances, rules, and common manufacturing checks. Define the entire mold structure, including the core, cavity, component systems and mold base for both prototype and production-scale multi-cavity molds.
Technology that enhances hygiene and safety – Hindware launches new ‘Easy Clean’ washbasins
Mixing the available materials with alloys or blends of previously developed materials enables product designers to choose from a vast range of materials to find the one with exactly the right properties. Although injection molding is one of the most cost-effective manufacturing options, it does have one drawback. It requires a significant capital investment and a relatively long lead time to machine the tools. After molds have been machined, design alterations can be very expensive or sometimes impossible without completely replacing the mold. This is why the design must be near perfect before the CAD files are released for machining. A comprehensive understanding of the basic principles of tool design is, therefore, very beneficial in avoiding costly problems and project delays.
Injection Mold Design Process
They are manually removed from the mold during the part ejection process. The example above shows a gate location centrally located for uniform material flow and hidden by a removable battery cover. This is one method of locating gates on cosmetic surfaces that solves two problems — optimizing material flow and providing a gate location that will not adversely affect part appearance.
SpaceX is launching more rockets from a military base. Can the Coastal Commission impose a limit?
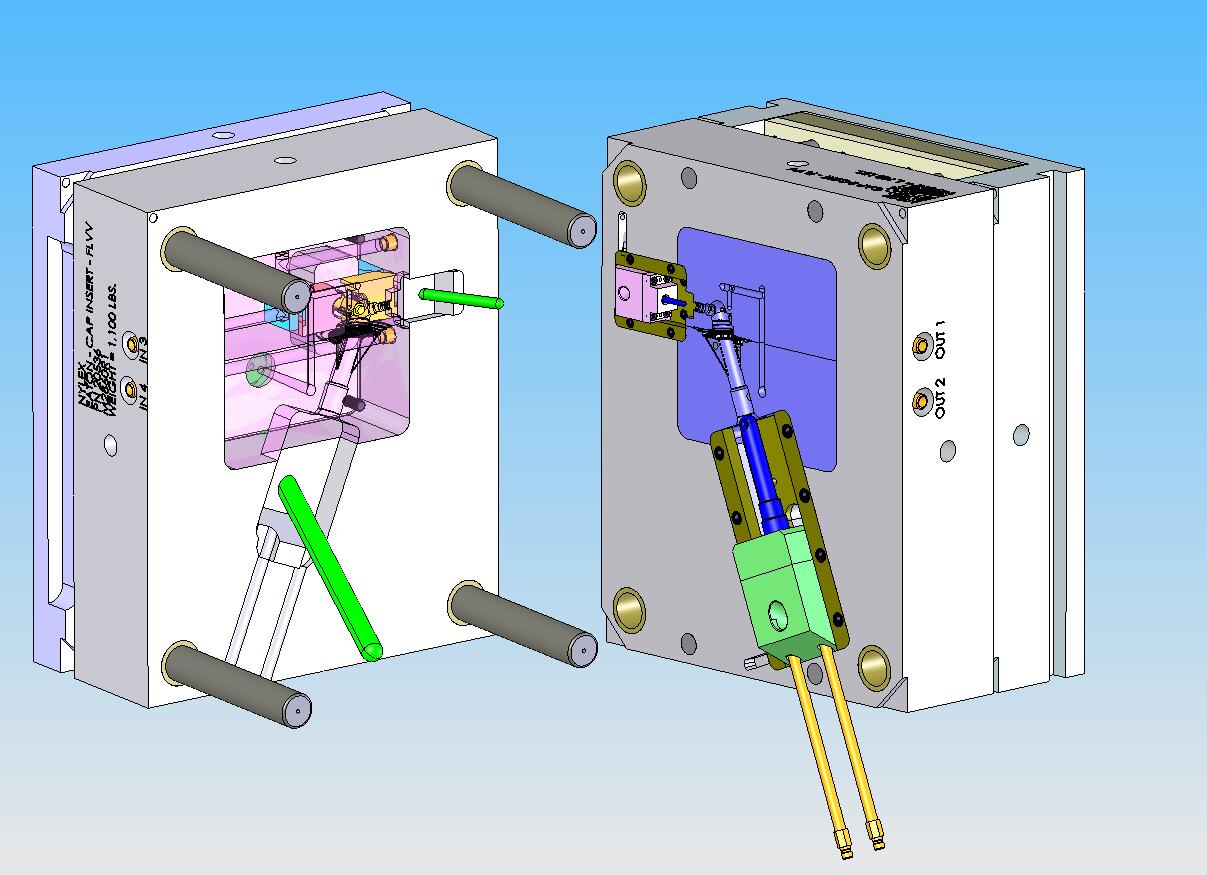
In this section, you’ll learn more about the key characteristics of the most popular materials. We’ll also discuss the standard surface finishes that can be applied to injection molded parts. The recommended minimum production volume for injection molding is 500 units.
Advances in resin 3D printing you should put to work today - Medical Design & Outsourcing
Advances in resin 3D printing you should put to work today.
Posted: Thu, 21 Dec 2023 08:00:00 GMT [source]
For plastic parts, you can read our guide to manufacturing processes for plastics. More complex designs, like this cap with a thread and undercuts, often require multi-part molds, with inserts or side-action cores. Tool construction is verified and the process is detailed and documented so it can be used in the future with minimal setup time.
Core and cavity development
When the interior of a part solidifies before its surface, a small recess in an otherwise flat surface may appear, called a sink mark.Parts with thick walls or poorly designed ribs are most prone to sinking. In comparison, parts made in a desktop 3D printer can be ready for delivery overnight, while industrial 3D printing systems have a typical lead time of 3-5 days. CNC machined parts are typically delivered within 10 days or as fast as 5 days. Side-action cores are moving elements that enter the mold from the top or the bottom and are used to manufacture parts with overhangs (for example, a cavity or a hole). Side-actions should be used sparingly though, as the cost increases rapidly. CNC machines for mold making use solid bodies to produce quality and cost-effective products.
The experiment involves injecting a light-activated resin into a 3D printed mold of a Lego brick. The goal is to compare the physical and chemical properties of the object created in space with those of an identical object created on the ground. Our product developers and engineers have 20+ years of experience in the industry.
We've learned from experience that, before production begins, there are important design elements to consider. These may improve the moldability of the parts, and ultimately, may reduce the chance of production hiccups, cosmetic defects and other issues. Depending on your design, you might need a one-piece or two-piece mold. The processes for making these molds are similar, but it will take a bit longer to create a two-part mold. Use the step-by-step instruction in the video or our practical guide to making silicone molds to create your own molds.
In 1869, John Wesley Hyatt invented celluloid, the first practical artificial plastic intended to replace ivory for the production of… billiard balls! Early injection molding machines used a barrel to heat up the plastic and a plunger to inject it to the mold. In this guide you’ll find everything you need to know about injection molding. Master the technology’s basic principles and learn actionable design tips fast that will save you time and cut costs. When the hot melt flows into the injection mold, the thick sections don’t cool as fast as the rest of the part because the thicker material becomes insulated by the outside surface of faster cooling plastic.
This episode is brought to you by ISCAR with New Ideas for Machining Intelligently. The Mold Design teaching team takes this opportunity to acknowledge the support of Dassault System, Autodesk and Mastercam, for the continuous support with educational licenses of state-of-the-art CAD, CAE and CAM, software. The contribution of these companies to the education of Plastics Engineers at UMass Lowell continues to make the difference. The delivery of the virtual class was made possible by the use of Zoom for online meetings, and of Camtasia for video editing of the lecture recordings. Download our white paper to learn about six mold-making processes that are possible with an in-house SLA 3D printer, illustrated with real-life case studies. Though all metal casting techniques share the same core process, there are various methods better suited for different applications.
This allows a freeze point between the part and runner removing the heat from the surface of the part. You want the heat removed from this surface to minimize any risk of sink in the part. After molding, the tab gate needs to be manually removed leaving a gate vestige within 0.005 in. When the pandemic arrived, teaching a hands-on design class and making it a significant virtual experience for students posed many challenges. The teaching staff had to work hard to pivot the class—with one week’s notice—into a rigorous and interactive design experience.
At this point economies of scale start to kick-in and the relatively high initial costs of tooling have a less prominent effect on the unit price. Gates vary in size and shape depending upon the type of plastic being molded and the size of the part. Large parts will require larger gates to provide a bigger flow of resin to shorten the mold time. Small gates have a better appearance but take longer to mold or require higher pressure to fill correctly.
He had a passion for perfection and excellence that has become our benchmark. We carry on this tradition as first generation molders and third generation mold makers. Use the motion simulation capabilities to verify the entire range of movements of the mold, including dynamic collision detection. Parts with different geometries can also fit in the same mold (remember, the model airplane example). The Society of Plastics Industry (SPI) explains several standard finishing procedures that result in different part surface finishes. Thermoset with excellent heat & chemical resistance and customizable shore hardness.
Under expert surveillance, we ensure your product prototyping and production turnaround are error-free. With 2D & 3D design, we can help our clients figure out changes or improvements needed for the product. We can check all the details in the mold and avoid the possibility of mistakes. We can provide your company with precision tooling to meet your specific application.
Teams generated multiple CAD iterations using Solidworks to assemble components into the standard mold. Then, using CAE tools provided by Autodesk Moldflow, students were able to run complete cool, fill, pack and warp injection molding simulations. Their focus was on gate location and flow analysis for defect detection/prevention, warpage mitigation and cycle time optimization. Subsequent discussion of simulation results with the teaching team helped teams iterate their designs and optimize solutions. The mold is the foundation of the whole injection molding process hence building it requires high precision.
No comments:
Post a Comment